Category
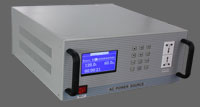


Frequency Converters Make Motors More Reliable
Induction motor systems consume approximately 65 percent of the $33 billion spent each year on electricity by domestic manufacturers. More than half of these induction motors are used in either fan or pump applications. This is why so many manufacturers are looking at frequency converters to reduce the power consumed in fan and pump applications. In fact, the physical size and, more importantly, the cost of converters have been reduced to levels where the payback in many instances is quite often one year or less!
Are you currently controlling the air flow within your existing Air Handling Units (AHU) with inlet or outlet dampers? Are you currently controlling the flow of water or other fluids by adjusting valve position? If your answer to either of these questions is YES, then your facility is an ideal candidate for the use of frequency converters. Frequency converters are one of the most overlooked devices for providing energy savings within your facility. Did you know that an electric motor running at 50% speed on the type of system described above only requires approximately 12.5% of the energy required to run it at full speed? With the rebates now being offered by many of the utility companies for the installation of energy saving devices, the payback for the entire installation including labor is quite compelling. On many systems the payback for the frequency converter is less than a year!
Take a look at the chart below. A one year payback is the equivalent of a 100% return on investment!
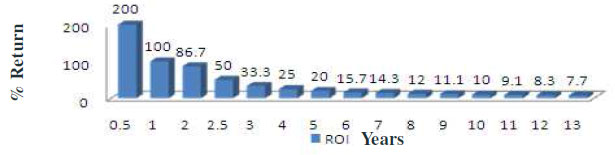
Energy savings, which can be substantial, is not the only benefit of the installation of frequency converters, there are also additional savings realized in the reduction on wear and tear on the equipment. This savings, also significant, is not taken into consideration in the payback period described above.
While frequency converters can provide your facility with substantial energy savings, they do present some special considerations to insure reliable and trouble free installation. While frequency converters inherently correct bad power factor, they are a switching power supply and can induce harmonics into your system. Converters take Alternating Current (AC) and convert it to a pulse width modulated DC output. These are pulses of DC of varying duration that the induction motor interprets as AC. Any equipment that switches from AC to DC such as the power supply on your laptop, ballasts in fluorescent light fixtures, UPS systems and the frequency converter can cause stray voltages and/or currents called transients or harmonics to be fed back into the voltage supply. These stray voltages can lead to problems with other electronic equipment as well as the frequency converter itself. Induction motor and conductor overheating and bearing damage are some symptoms of transients. Newer frequency converters utilizing the latest electronic components induce far less than their predecessors but precautions should still be taken to reduce the likelihood of induced harmonics. Frequency converters are also susceptible to existing harmonics that may already be in your electrical system. To help prevent the frequency converter from creating these transients, there are some precautions that should be taken. The installation of an appropriately sized line reactor installed on the input side of the frequency converter can help prevent transients formed within the frequency converter from being fed back into the incoming power feed as well as blocking any transients on the incoming feed from entering the frequency converter. These are relatively inexpensive one-to-one transformers rated by load and impedance.
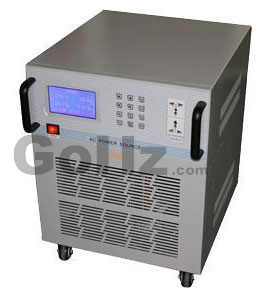
On the output side of the frequency converter are three possible areas of concern. The first lies within the motor itself. The windings in older motors, those not inverter duty rated, were insulated with a varnish that may not react favorably to the pulses and voltage spikes created by the frequency converter. These voltage spikes may be of a magnitude that will eventually break down the insulation on the windings within the motor. The induction motor will overheat and eventually fail. Higher efficiency, inverter duty rated motors have windings insulated to accept these voltage spikes without breaking down.
These transient voltages within the motor need to go somewhere and the natural path is through the shaft, into the bearings and then to ground through the motor casing. Here lies the second possible problem area at the induction motor. As these voltages and currents pass from the motor shaft to ground, they have to pass through the bearings inside the bearing races.
Once these voltages exceed the resistance of the bearing lubricant, they discharge through the motors bearings causing pitting, fluting damage, excessive bearing noise and eventual bearing failure. Grounding rings are available for installation on the induction motor shaft which prevent electrical bearing damage by safely channeling harmful shaft voltages away from the bearing to ground. These rings provide the path of least resistance to ground and dramatically extend motor life.
This brings us to the third potential area of concern, long lead length between the frequency converter and the induction motor. As a rule of thumb, the distance between the frequency converter and the induction motor should not exceed 75 to 100 feet. Greater distance can cause reflected or standing wave phenomenon and capacitive coupling.
This phenomenon has a voltage doubling effect at the motor terminals. In fact, the voltage spikes mentioned earlier created by the frequency converter can reach the 1300V range causing motor deterioration and eventual failure.
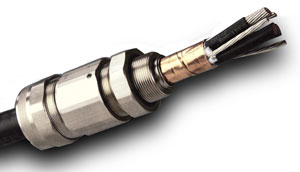
The voltage build up caused by the capacitive effect of these long lead lengths can also have an adverse effect on the frequency converter and can cause nuisance tripping within the frequency converter and cause overheating in both the frequency converter and the induction motor significantly reducing the life of either or both. There are a couple of precautions that can be taken to help prevent these issues. First, a load reactor can be installed on the output side of the frequency converter. Just as the line reactor on the input side helps prevent transients from entering or exiting the frequency converter on the line side, the load reactor provides the same results on the output side of the frequency converter. Specialized cable is also available to help counteract these problems as well as reduce the introduction of stray voltages and currents into these conductors from external sources.
As mentioned in the beginning, as long as they are properly installed and the appropriate precautions taken, frequency converters are and excellent way to save energy, reduce maintenance and downtime on pump and fan installations.
If you would like more information, help with sizing and selecting the appropriate frequency converter for your application or help with the precautionary equipment described, please contact your local Springfield Electric representative.
Are you currently controlling the air flow within your existing Air Handling Units (AHU) with inlet or outlet dampers? Are you currently controlling the flow of water or other fluids by adjusting valve position? If your answer to either of these questions is YES, then your facility is an ideal candidate for the use of frequency converters. Frequency converters are one of the most overlooked devices for providing energy savings within your facility. Did you know that an electric motor running at 50% speed on the type of system described above only requires approximately 12.5% of the energy required to run it at full speed? With the rebates now being offered by many of the utility companies for the installation of energy saving devices, the payback for the entire installation including labor is quite compelling. On many systems the payback for the frequency converter is less than a year!
Take a look at the chart below. A one year payback is the equivalent of a 100% return on investment!
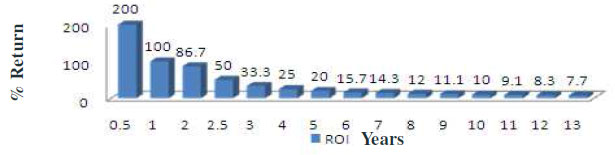
Energy savings, which can be substantial, is not the only benefit of the installation of frequency converters, there are also additional savings realized in the reduction on wear and tear on the equipment. This savings, also significant, is not taken into consideration in the payback period described above.
While frequency converters can provide your facility with substantial energy savings, they do present some special considerations to insure reliable and trouble free installation. While frequency converters inherently correct bad power factor, they are a switching power supply and can induce harmonics into your system. Converters take Alternating Current (AC) and convert it to a pulse width modulated DC output. These are pulses of DC of varying duration that the induction motor interprets as AC. Any equipment that switches from AC to DC such as the power supply on your laptop, ballasts in fluorescent light fixtures, UPS systems and the frequency converter can cause stray voltages and/or currents called transients or harmonics to be fed back into the voltage supply. These stray voltages can lead to problems with other electronic equipment as well as the frequency converter itself. Induction motor and conductor overheating and bearing damage are some symptoms of transients. Newer frequency converters utilizing the latest electronic components induce far less than their predecessors but precautions should still be taken to reduce the likelihood of induced harmonics. Frequency converters are also susceptible to existing harmonics that may already be in your electrical system. To help prevent the frequency converter from creating these transients, there are some precautions that should be taken. The installation of an appropriately sized line reactor installed on the input side of the frequency converter can help prevent transients formed within the frequency converter from being fed back into the incoming power feed as well as blocking any transients on the incoming feed from entering the frequency converter. These are relatively inexpensive one-to-one transformers rated by load and impedance.
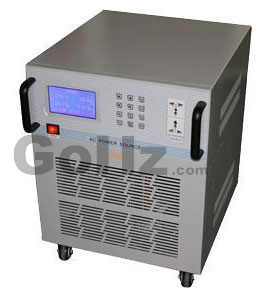
On the output side of the frequency converter are three possible areas of concern. The first lies within the motor itself. The windings in older motors, those not inverter duty rated, were insulated with a varnish that may not react favorably to the pulses and voltage spikes created by the frequency converter. These voltage spikes may be of a magnitude that will eventually break down the insulation on the windings within the motor. The induction motor will overheat and eventually fail. Higher efficiency, inverter duty rated motors have windings insulated to accept these voltage spikes without breaking down.
These transient voltages within the motor need to go somewhere and the natural path is through the shaft, into the bearings and then to ground through the motor casing. Here lies the second possible problem area at the induction motor. As these voltages and currents pass from the motor shaft to ground, they have to pass through the bearings inside the bearing races.
Once these voltages exceed the resistance of the bearing lubricant, they discharge through the motors bearings causing pitting, fluting damage, excessive bearing noise and eventual bearing failure. Grounding rings are available for installation on the induction motor shaft which prevent electrical bearing damage by safely channeling harmful shaft voltages away from the bearing to ground. These rings provide the path of least resistance to ground and dramatically extend motor life.
This brings us to the third potential area of concern, long lead length between the frequency converter and the induction motor. As a rule of thumb, the distance between the frequency converter and the induction motor should not exceed 75 to 100 feet. Greater distance can cause reflected or standing wave phenomenon and capacitive coupling.
This phenomenon has a voltage doubling effect at the motor terminals. In fact, the voltage spikes mentioned earlier created by the frequency converter can reach the 1300V range causing motor deterioration and eventual failure.
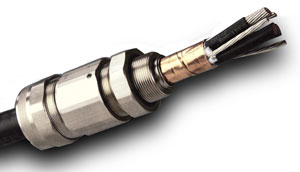
The voltage build up caused by the capacitive effect of these long lead lengths can also have an adverse effect on the frequency converter and can cause nuisance tripping within the frequency converter and cause overheating in both the frequency converter and the induction motor significantly reducing the life of either or both. There are a couple of precautions that can be taken to help prevent these issues. First, a load reactor can be installed on the output side of the frequency converter. Just as the line reactor on the input side helps prevent transients from entering or exiting the frequency converter on the line side, the load reactor provides the same results on the output side of the frequency converter. Specialized cable is also available to help counteract these problems as well as reduce the introduction of stray voltages and currents into these conductors from external sources.
As mentioned in the beginning, as long as they are properly installed and the appropriate precautions taken, frequency converters are and excellent way to save energy, reduce maintenance and downtime on pump and fan installations.
If you would like more information, help with sizing and selecting the appropriate frequency converter for your application or help with the precautionary equipment described, please contact your local Springfield Electric representative.
Post a Comment:
You may also like: